Abstract
Since 2015, the School of Oral Health Care at the University of Copenhagen has been tracking practically all dental instruments with an automatic wireless system based on RFID-technology. Instruments are tracked from the time they are dispensed throughout utilization, processing, sterilization and return to storage. With the cloud based server, staff has full control over the infection control status and stock levels of all instruments at all times. This enables continuous improvement in daily operations, long term planning and patient safety.
The Internet of Thing in Dentistry – from a vision to reality
A late afternoon in the autumn of 2010, Bo Danielsen sat in his office at the University of Copenhagen where he had recently been appointed Head of the School of Oral Health Care. He was looking at the budget for the following year and felt a little bit uneasy despite everything being OK. The school and clinic were running smoothly, the budget was balanced and he felt rather confident that next year everything would run as smoothly as before. However Bo wanted staff to use their time on teaching students and have concern for the patients – value added activity rather than on spending time in the sterilization room and on making inventory reports and budget estimates. In addition Bo also wanted information regarding the use of instruments, their utilisation and turn over in the clinics for fact based decision making regarding the manpower assigned the sterilization room and the need for renewal of instruments.
Despite the impeccable work the team had done, they still didn’t know exactly how much money they needed to spend on purchasing new mouth mirrors, curettes and other dental hand instruments that would wear out the next year as a result of normal wear and tear and regular sharpening. Previously they had also estimated renewal of instruments on pure intuition rather than on facts. The wish was to estimate the number of extra instruments needed for compensating the fact that all instruments are not always in the right place at the right time and that at any given time, a number of instruments are in the autoclave, some are in other phases of the reprocessing cycle and some are worn out. The team knew that the demand for instruments varied from day to day depending on the amount of treatments scheduled for that particular day and on the type of clinical procedures of those treatments. The team also knew that the capacity of the reprocessing section varies somewhat. Manning of the sterilization room and what to do when staff are sick is sometimes difficult when the need for capacity is not known in detail.
Bo knew that misplaced instruments was a wasteful hidden cost. Sometimes staff and students had to go from one operatory to the other to get an instrument that they had run out of. Not necessarily because there weren’t enough instruments but because the instruments were not in the right place at the right time. It is easy to disregard the time spent on this trivial task but every footstep taken in this situation is expensive. In addition to staff frustration and longer patient wait times, each footstep also means that the capital invested in the facilities and the dental delivery unit are running on idle and the time of the students is spent on something else than treating patients and learning. The cost per patient and cost per student was thus increased because of time wasted in inefficient processes. What annoyed Bo was that he didn’t know how big this impact on cost was and how much more could be done with the same resources if everything was optimized and the processes designed to help the staff and students do their jobs better.
Although everything was OK in the big picture, the tech savvy team in Copenhagen had never been complacent as far as continuous improvement goes. Previous brainstorming sessions had yielded ideas about how wireless tracking of instruments would change both how they did budgeting and how they ran daily operations at the clinic.
Five years later, on August 18th 2015, Danielsen walked through the main entrance of the Panum building. He had walked through these doors every day since he started working at the University of Copenhagen but today, he was stepping into the world’s first dental clinic and school with an RFID-based (radio-frequency identification) wireless tracking system for dental instruments. Together with LM-Dental, a company based in Finland and a part of the largest privately owned dental conglomerate Planmeca, Bo Danielsen and his team had implemented what previously had only been an idea. Now every dental delivery unit at the School of Oral Health Care was equipped with a wireless RFID-reader and additional readers were placed e.g. next to the autoclave in the reprocessing room and in storage rooms that serve different parts of the clinic. Practically all instruments ranging from mouth mirrors and aspirating syringes to dental turbines and micromotor handpieces were equipped with a tiny, autoclavable RFID-tag that is read wirelessly in an instant without slowing down the daily routines at the clinic. When Bo sat down at his computer, he logged-in to the cloud based server, the brains of the LM-Dental Tracking System (DTS), which receives all the information from all the readers across the clinic. On his screen he could see where each and every instrument was and whether it was ready for clinical use or contaminated and awaiting reprocessing. The complete history of the specific instrument in question is also documented including e.g. the information about when it was autoclaved and by whom.
Continous improvement and strive for efficiency
Today, thousands of events are logged each month. Dental chairside assistants Malene Nielsen and Nanna Sørensen find DTS easy and fast to use. Anyone from Bo’s team at the University of Copenhagen can log in anytime to the DTS-server and view the data from the perspective of their role and responsibility. When budgeting, for example a statistical report can be compiled to see what percentage of e.g. turbines have been used and autoclaved more than 250 times and may need to be replaced during the following year. On the other hand, the person responsible for the logistical operation of the clinic, can run report in the afternoon to see the current inventories of ready to use instruments and based on that decide what instruments need to be delivered to different storage rooms or operatories before the end of the day to be ready in the morning. With daily monitoring of stock levels, it is possible to make sure the right amount is available at every operatory and on the other hand that stockpiles are not gathered unnecessarily. Yet another aspect is that teachers can make sure that a student has returned all the instruments given to him or her – just like the university library keeps track of what books a student has forgotten to return. Likewise the instruments a student has or hasn’t used in a clinical simulation exercise can be tracked in order to give timely feedback if a vital step is misunderstood.
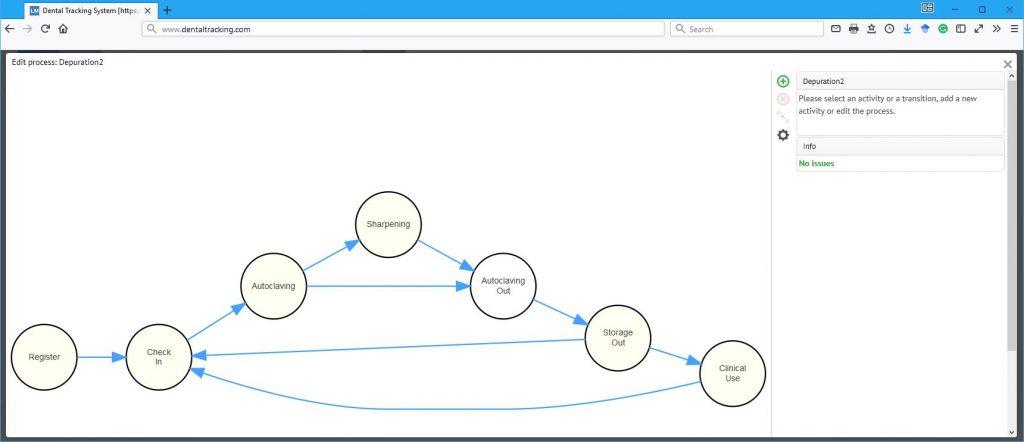
The next level of patient safety and clinical education
Infection control and patient safety is on a very high level in Denmark. However, wherever there is room for human error you should strive to create a system that makes it easy for those mistakes to surface and be dealt with in a constructive manner. With DTS, an additional layer of automatic safety checks is added without adding any administrative burden on the maintenance and clinical staff. When an instrument is read with a DTS reader, it automatically checks the status of that particular instrument and gives an alert if it isn’t appropriate for clinical use e.g. because the sterile shelf life has expired. Likewise a maintenance reminder can be set to make sure that curettes are sharpened and handpieces lubricated as planned.
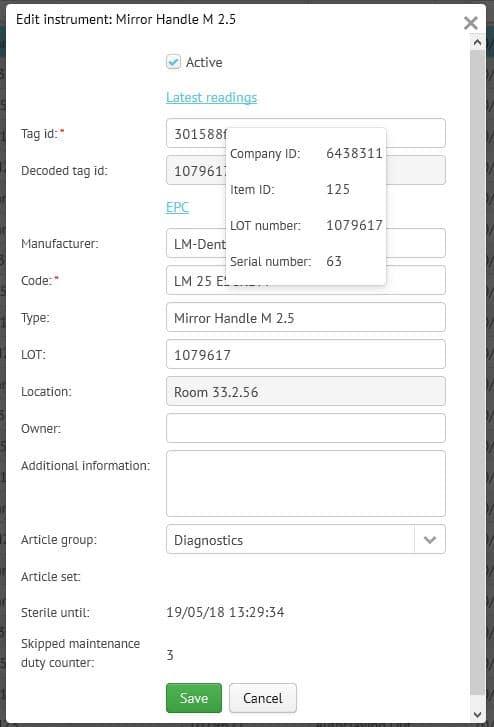
What is the LM-Dental Tracking System?
The LM Dental Tracking System™ (DTS) is the first commercially available system in the dental industry to efficiently track and monitor dental instruments and materials using RFID technology. Instruments, handpieces, filling materials, implants etc from different manufacturers are wirelessly read in few seconds. The system uses the RFID UHF (ultra high frequency) standard and EPC gen2v2 coding in order to make it possible to read many items in a single read in a few seconds. This means that e.g. a batch of 20 instruments can be read in a single step without causing any delays in daily routines.
The DTS-readers enable tracking of instruments, handpieces and implant etc from storage and maintenance through to clinic and patient care. The readers are available in two different models: Tray Reader with batch read functionality and Unit Reader for single-read options. Both readers communicate over Ethernet or WiFi to the DTS Server through encrypted communication. The readers can be configured to record single or multiple activities depending on the customer’s needs and can be placed anywhere with minimal footprint. Every time an item is read, the reader checks the database to see if any alerts need to be given to the user on the basis of the workflow and alerts defined for the clinic in question. The readers have been design to be simple and quick to use without extensive training.
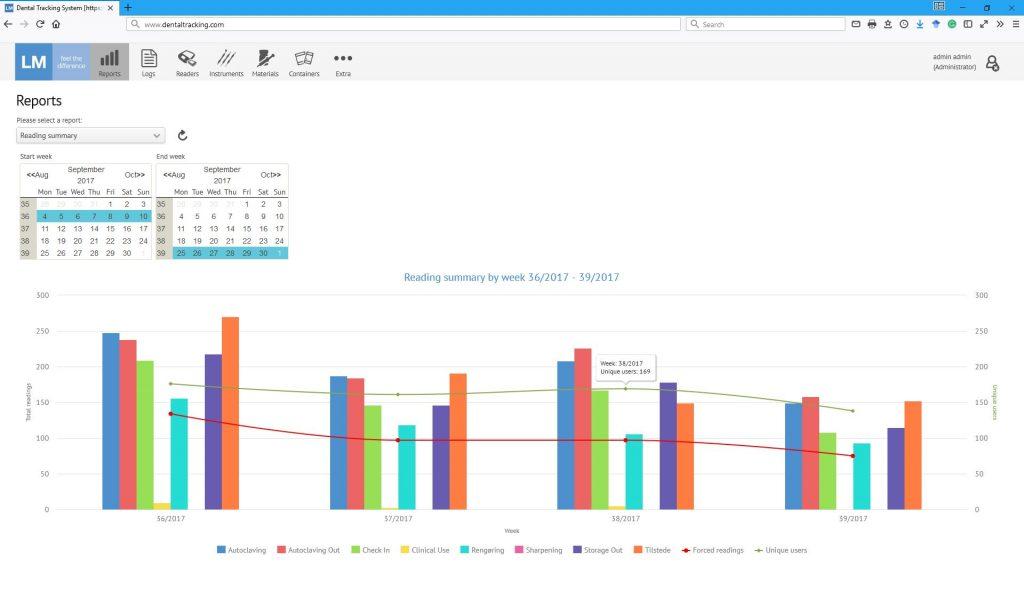
The cloud server is the brain of DTS and both configures the entire system and gathers all the data from all the readers. The administrators of a clinic can define what workflows are required for different article types, what alerts and reminders are given to users in different situations and what rights different users have. The big data gathered from all the readers into the cloud server can be used in many different ways depending on the needs of the clinic in question:
- asset management
- process optimization
- infection control documentation for each instrument
- simulated (phantom) and clinical education
By logging in to the system, users can easily browse reports and view statistics to e.g.:
- check the location and status of every instrument including its infection control history
- see the stock levels at different departments, dispensaries and rooms for anything from handpieces to gloves
- check for expiring materials
- benchmark the consumption of materials and logistic rotation of instruments
- analyze processes and optimize for efficiency
- locate missing items and control loss of assets
- allocate cost by patient, clinician, room or department for accurate accounting and budgeting
- review student work, verify competence and to provide timely guidance and feedback
Compatibility through open standards
Anything at a dental clinic can be connected to DTS. The LM Dental Tracking System™ offers compatibility with instruments, handpieces and materials etc from different manufacturers. Any product with an RFID tag using UHF and EPC gen2v2 is compatible with LM Dental Tracking System™.
An API enables communication between DTS and Patient Information Management Systems, Clinic Management Systems, ERP-systems etc. The API also makes it possible for RFID readers from other manufacturers to be connected to the LM Dental Tracking System™. Hardware modules for integrating DTS into equipment and consultation regarding RF-measurements, RFID tag placement and fastening solutions are also available for both manufacturers and clinics.
DTS also supports the Global Location Number (GLN) standard which allows for uniquely identified locations and rooms in different departments, buildings and geographical locations. If two dental chains are combined as the results of an acquisition or a merger, the GLN allows the DTS system to combine the two DTS-servers into one single server without renaming or renumbering any rooms or locations.
UDI adds value to DTS
The Unique Device Identifier (UDI) system and the Global UDI Database (GUDID) maintained by the FDA as well as the European Database on Medical Devices (EUDAMED) or other national authorities can provide additional value to DTS. All medical devices having a machine readable UDI that meets the GS1 standards and uses UHF RFID tags with EPC gen2v2 coding can be read with DTS to obtain the data from the GUDID database using the GUDID Device Lookup API.
Conclusion
The combination of having an autoclavable RFID tag on each instrument, using UHF RFID readers and storing all data in the LM-Dental Tracking System cloud, allows the School of Oral Health Care at the University of Copenhagen to both continuously improve their daily operations, use technology to support education, improve long term planning and budgeting and obtain big data that can be used for analysis and research purposes.