Authors: Valter Rönnholm and Bo Danielsen
Source: GS1 Healthcare Reference Book 2018-2019
LM-Dental™, a leading manufacturer of dental products based in Finland, is implementing GS1 standards across its entire product portfolio, starting with dental hand instruments. Drivers for these efforts include the US Food and Drug Administration (FDA) Unique Device Identification (UDI) regulation. Since 2015, LM-Dental has applied EPC-enabled RFID (Radio Frequency Identification) technology and GS1 identifiers to its dental hand instruments. LM-Dental’s customers (e.g., hospitals, universities and dental clinics) can now partner with them to track dental instruments with an automated traceability system—the LM-Dental Tracking System™ (DTS), using GS1 standards. Instruments are tracked from the time they are dispensed through to utilization, processing, sterilization and return to storage. The University of Copenhagen’s School of Oral Health Care is one such hospital that has leveraged LM-Dental’s use of GS1 standards to make continuous improvements in its daily operations and long-term planning for increased patient safety. With GS1 standards, the school’s staff has greater control over the infection control status and stock levels of all instruments, reducing inventory costs by approximately 10 percent.
The perspective of the hospital
On a late afternoon in autumn 2010, Bo Danielsen sat in his office at the University of Copenhagen where he had recently been appointed head of the School of Oral Health Care. He was reviewing the school’s budget for the following year and felt a bit uneasy. The school and clinic were operating smoothly, the budget was balanced and he felt confident that the next year would run as well as the year before.
Yet, Danielsen wanted his staff to spend their time teaching students and focusing on patients — on value-added activities rather than spending time in the sterilisation room and creating inventory reports and budget estimates.
“I felt we needed information about the utilisation of instruments and their turnover in the clinics to make fact-based decisions about the required staff assigned to the sterilisation room and the need for new instruments,” explains Danielsen. The school didn’t know exactly how much budget was needed for new mouth mirrors, curettes and other dental hand instruments that would eventually need to be replaced during the next year. In past years, Danielsen and his team had estimated the needed renewal of instruments based on intuition rather than data.
To estimate the number of extra instruments, several factors needed to be considered. First, all instruments were not always in the right place at the right time. At any given time, a number of instruments would be in the autoclave, some in other phases of the reprocessing cycle and some would need to be replaced. Secondly, the demand for instruments varied from day-to-day depending on the number of treatments scheduled and on the type of clinical procedures. Finally, the capacity of the reprocessing section varied. Resourcing the sterilisation room and developing contingent plans (e.g., when members of staff were sick) was difficult when the needed capacity was not known.
Danielsen also realised that misplaced instruments represented a wasteful, hidden cost. At times, staff and students had to go from one operating room to the other to get an instrument—not because there weren’t enough instruments but because the instruments were not in the right places, at the right time. It might have been easy to disregard the time spent on this trivial task, yet every footstep meant additional cost, a frustrated staff and
longer wait times for patients. It also meant that capital invested in the facilities and dental delivery unit was not being used wisely, and student time was spent on something other than treating patients and learning. In summary, the cost per patient and cost per student were inflated due to time wasted and inefficient processes.
“We didn’t know exactly ‘how big’ the impact of these inefficiencies had on costs and how much more could be done with the same resources, if processes were optimised,” says Danielsen. “Previous brainstorming sessions had yielded ideas about how the wireless tracking of instruments could change both how we developed the budget and how we ran our daily operations at the clinic. In the spring of 2015, we decided to take action.”
From vision to reality
By collaborating with LM-Dental, part of the largest privately owned dental conglomerate, Planmeca, Danielsen’s vision was soon to become a reality.
“The development of DTS started in 2011 when a strategic decision was made to develop further the LM-Dental hand instrument offering with a new handle design and to include intelligence in the instrumentation. The target to add intelligence into instruments initiated an in-depth analysis of latest technologies to enable data migration and storage related to the use of an individual instrument. After research and tests LM-Dental found UHF EPC/RFID as the optimal technology for the purpose. “We soon realised that in order to be complete, this system needed to read and track not only our own instruments but also all moving valuable items and materials in the clinic,” explains Timo Helenius, CEO of LM-Dental.
The R&D team at LM-Dental was aware that the organisation needed to meet the requirements of the US FDA’s UDI legislation and chose GS1 as its ssuing agency. The UHF RFID technology, using GS1 EPC/RFID standards proved to be most suitable for wireless tracking of instruments and materials in dental environments. LM-Dental was also in the process of planning an organisationwide UDI implementation.
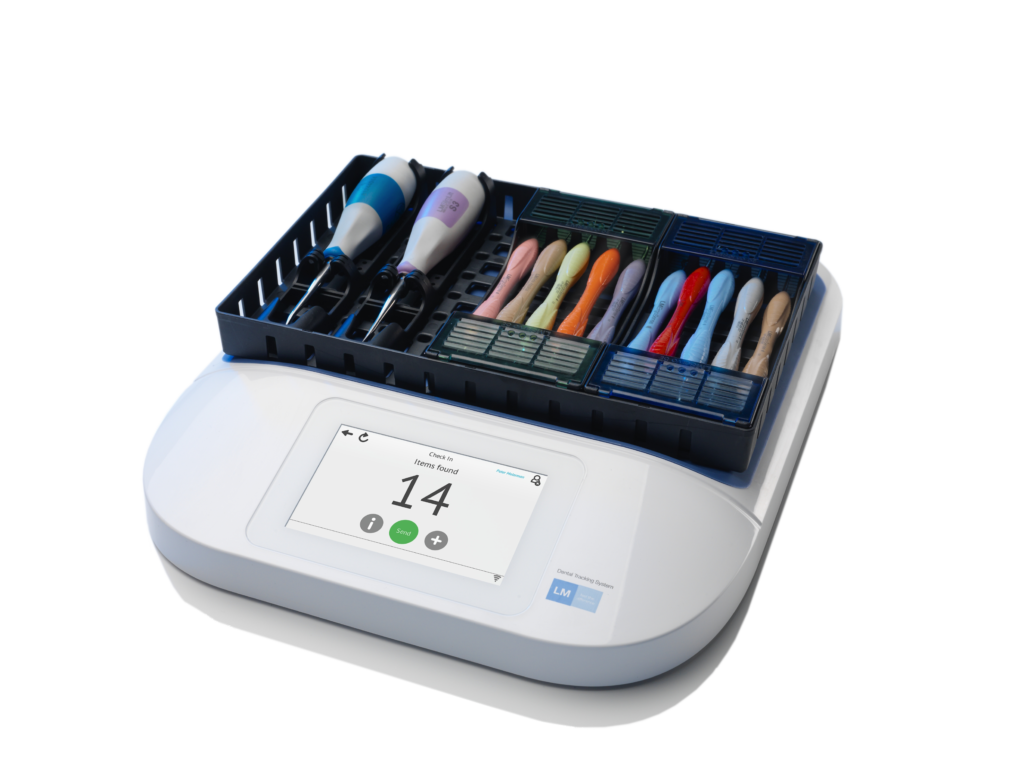
After listening to customers, LM-Dental worked to ensure that the first stage of the LM-Dental UDI project focused on dental hand instruments as part of the LM-Dental portfolio. This meant that LM-Dental moved ahead of regulatory requirements to provide unique identification and EPC/RFID marking. Now, every LM-Dental instrument is available with the option of being uniquely identified with a Global Trade Item Number® (GTIN®) and
serial number, encoded in a tiny EPC/RFID tag that can be wirelessly read in an instant without slowing down daily routines at the clinic. Likewise, aspirating syringes, dental turbines and micromotor handpieces are equipped with a tiny, autoclavable EPC/RFID tag. The University of Copenhagen School of Oral Health Care is equipped with an LM-Dental wireless RFID-reader at the point of delivery and additional readers are placed, for example, next to the autoclave in the reprocessing room and in storage rooms that serve different parts of the clinic.
Benefits for all stakeholders
While LM-Dental was driven to both develop a wireless tracking system and meet the regulatory requirements by using GS1 standards and UHFRFID, the identifiers and data carriers continue to provide value within LM-Dental’s own business processes. The company recognises that its efforts and UDIs are not only beneficial for customers, but also for its organisation, particularly as the implementation of GS1 standards for the full product portfolio continues to progress.
Certainly, for hospitals such as the one at the University of Copenhagen, the benefits are clear. When Danielsen sits down at his computer, he logs into the cloud-based server that receives all the information from readers that scan and collect information from the EPC/RFID tags on instruments across the clinic.
On my screen, I can see where each instrument is located and whether it is ready for clinical use or [is] contaminated and awaiting reprocessing. The complete history of the specific instrument is also documented, including information about when it was autoclaved and by whom.”
“On my screen, I can see where each instrument is located and whether it is ready for clinical use or [is] contaminated and awaiting reprocessing,” says Danielsen. “The complete history of the specific instrument is also documented, including information about when it was autoclaved and by whom.”
Gaining visibility, safety and facilitating education in the hospital
Today, thousands of instrument-specific events are logged each month. Dental Chairside Assistants, Malene Nielsen and Nanna Sørensen, find the new GS1 standards-based traceability system easy and fast to use. Anyone from the Danielsen team can view data from the perspective of his/her role and responsibility.
“When budgeting, we can get a statistical report to see, for example, what percentage of turbines has been used and autoclaved more than 250 times and, therefore, may need to be replaced during the following year,” advises Danielsen.
Also, the person responsible for the clinic’s logistics can run a report in the afternoon to review current inventories of ready-to-use instruments; and, based on inventory levels, decide which instruments need to be delivered to different storage rooms or operatories before the end of the day, for use the following morning. With the daily monitoring of stock levels, it is possible to ensure the right amount is available at every operatory and that stockpiles are not collected unnecessarily.
Another benefit: Teachers can ensure that students return all instruments given to them. Likewise, the instruments a student has or hasn’t used in a clinical simulation exercise can be tracked in order for teachers to give timely feedback, if a vital step was not taken and perhaps misunderstood.
“ With the new traceability system, we have the needed data to improve our daily operations, support education, improve long-term planning and budgeting, and obtain big data that can be used for analysis and research
Infection control and patient safety are top priorities in Denmark. “While there may be room for human error, you should strive to create a system that makes it easy for those mistakes to surface and be dealt with in a constructive manner,” says Danielsen. With the traceability system, a layer of automatic safety checks is added without any administrative burden on the maintenance and clinical staff. When an instrument’s GS1 identifier in the EPC/RFID tag is read, its status is automatically checked. An alert is given if the instrument isn’t appropriate for clinical use, for example, if the sterile shelf life has expired. Likewise, a maintenance reminder can be set to make sure that curettes are sharpened and handpieces are lubricated, as planned.
Vision to reality to tangible
benefits
“With the new traceability system, we have the needed data to improve our daily operations, support education, improve long-term planning and budgeting, and obtain big data that can be used for analysis and research purposes,” concludes Danielsen.
Specific benefits realised by the School of Oral Health Care include:
Several hours per week are saved by each staff member as they no longer have to search for misplaced instruments.
Just-in-time processes for instrument maintenance have reduced inventory costs by approximately 10 percent.
Visibility of utilisation count and maintenance reminders reduce the time needed for manual checking of instruments by more than 100 hours per year, for the 250,000 instruments sterilised per year. This is the equivalent of three person-weeks.
With the new traceability system, we have the needed data to improve our daily operations, support education, improve long-term planning and budgeting, and obtain big data that can be used for analysis and research purposes.”
Lessons learned
The collaboration between LM-Dental and the Universtity of Copenhagen has led to a highly successful implementation of GS1 standards to meet both the FDA UDI requirements while delivering significant benefits for the School of Oral Health Care.
Throughout the process, much has been learned by LM-Dental that will help to streamline future implementations and feed into the company’s project to implement GS1 standards for the remaining products.
Experience has also shown that marking UDI information in human-readable format can be challenging at times, depending upon the substrate used to produce surgical instruments. Therefore, the testing of different direct marking mechanisms is very important.
Overall, LM-Dental advises that understanding the need of customers should be a primary focus, given that clinics will need to make investments if they are to support traceability of products within their facilities.
Having open discussions to understand the current logistics flows within the clinic as well as the overall plans of the clinic and how the implementation of RFID technology for specific applications could fit into their longer term goals is key, particularly given the current overall industry trend for use of barcoding for UDI. When needing item-level traceability of LM-Dental instruments, the time-saving benefit of the multi-reading capability of UHF RFID has a significant impact on the daily manual handling times.
About the authors
Valter Rönnholm holds a M.Sc. in Communications Engineering from the Aalto University School
of Electrical Engineering. He has extensive experience in product development, product management, sales and marketing, ranging from industrial and consumer electronics to medical devices. He worked as Business Development Manager at LM-Dental.
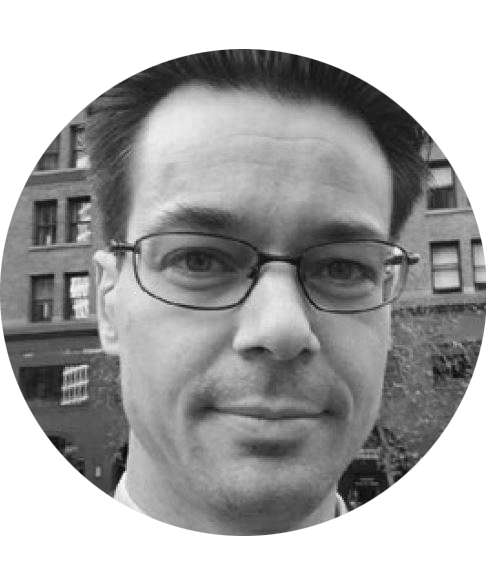
Bo Danielsen has extensive experience in clinical and educational administration as well as dentistry and particularly oral hygiene and periodontology. He is the head of the School of Oral Health Care at the University of Copenhagen in Denmark and the president of the Danish Society of Periodontology as well as the Danish Association for Dental Health Without Borders. He has a
degree in dentistry from the University of Århus in Denmark, a MBA from South Bank University, England, and a MIL from it-Vest, Denmark.
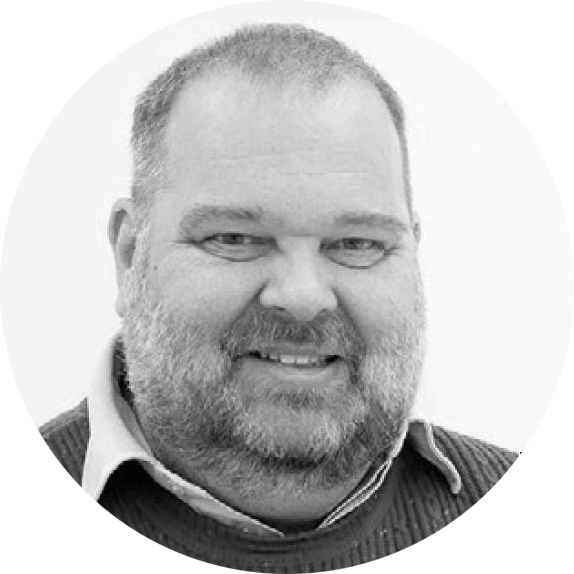